The automotive group Stellantis has announced a significant investment to double the production capacity of its Kenitra plant in Morocco. The focus of this innovation is a brand new paint shop, built in collaboration with the German company Dürr, a long-time expert in automotive industry technologies. And it is thanks to these newer, advanced technologies and the use of recycled robots that the new plant will make it possible to produce electric vehicles more efficiently and sustainably, reducing environmental impact.
A aew advanced painting process
The Stellantis aims to double production at its Moroccan factory in Kenitra by introducing an innovative paint shop designed by Dürr and to meet the growing demand for electric vehicles.The new Dürr paint shop, located in the northwestern region of Morocco, represents a significant step forward in sustainable automotive production. Designed to optimize energy consumption, this state-of-the-art facility will enable Stellantis to significantly increase production of electric and hybrid vehicles for its Peugeot, Citroën, and Fiat brands. In particular, the paint line has been designed to operate with maximum efficiency, processing up to 30 bodies per hour, matching the productivity of the first plant built by Dürr in Kenitra in 2019.
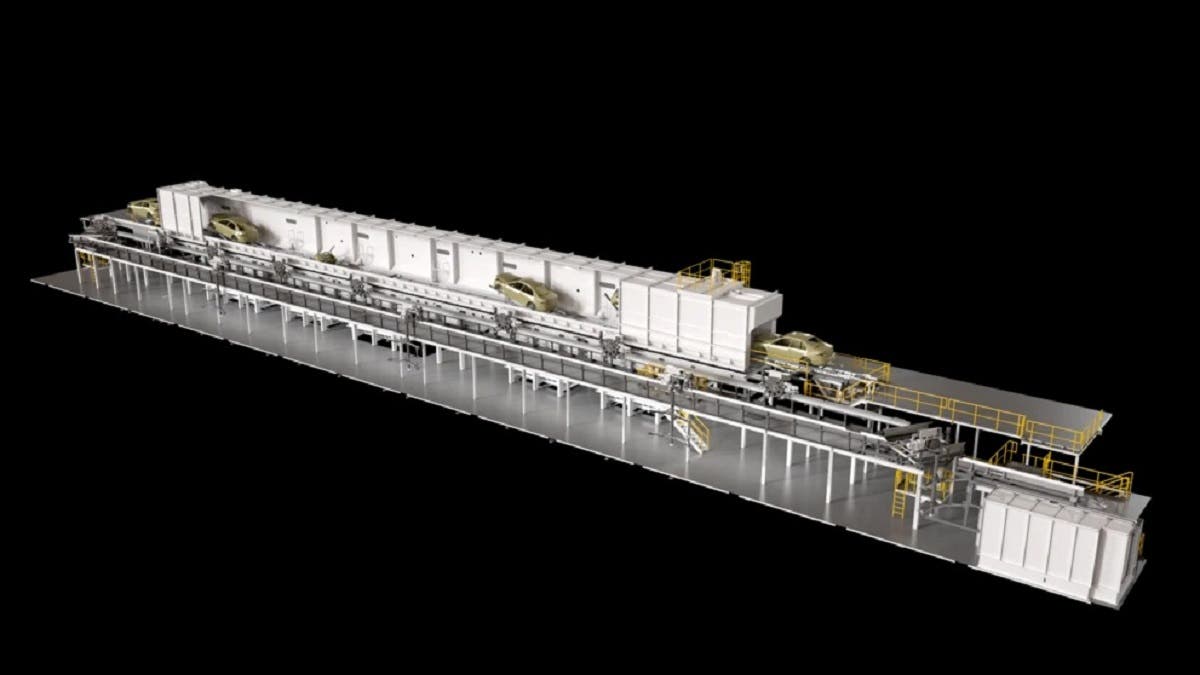
The heart of this new state-of-the-art vehicle painting department lies in Dürr’s RoDip system. This patented technology allows for highly efficient pre-treatment and protection of car bodies. Thanks to a new transport system, RoDip significantly reduces the consumption of water, chemicals, and energy. At the same time, this technology guarantees excellent corrosion protection.
This new, highly advanced plant is a model of energy efficiency and sustainability, designed specifically to meet the needs of hybrid and electric vehicles. Stellantis’ decision to use refurbished robots from other plants, combined with the choice of innovative technologies, demonstrates the automotive group’s strong commitment to minimizing environmental impact and optimizing the use of available resources.
Integrated Approach to Stellantis’ Sustainability Goals
Another important element used for this change is Dürr’s EcolnCure electric oven. This tool allows for even and rapid heating and cooling of vehicle bodies. This factor significantly reduces production times and the thermal stress generated on the structures during this phase. Furthermore, the use of electricity from renewable sources has also significantly reduced CO2 emissions compared to the use of traditional gas ovens.
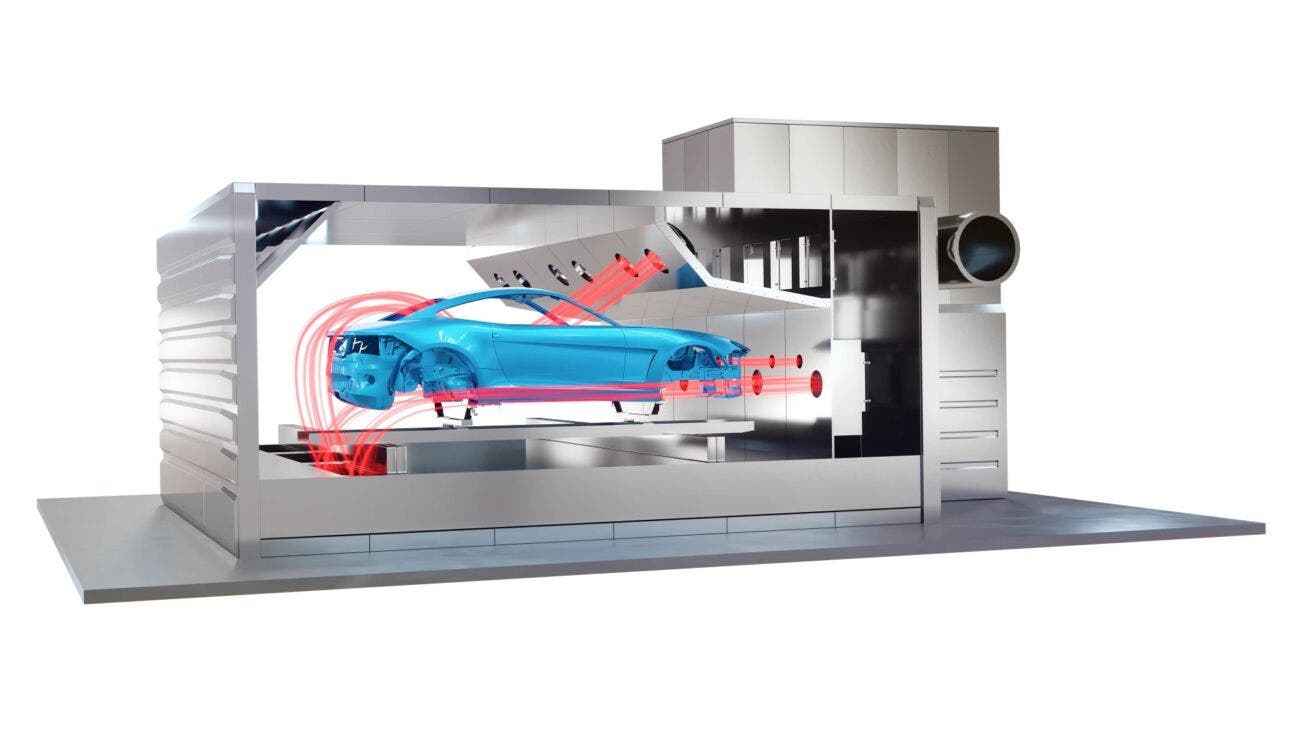
Stellantis has also adopted a holistic approach to the design of the new plant. This means that the company has decided to prioritize the reuse of existing materials and equipment, without the need to create new ones specifically. We are talking about robots, air supply systems, and conveyor belts that come from Stellantis plants currently located in Europe. These have been transported and refurbished to Kentira, a factor that has significantly contributed to reducing costs and, above all, the time required to complete such a project. In fact, waiting for the creation of specific equipment would have required a very long time to activate this process, which the current market situation cannot afford.
Stellantis’ decision to expand its Moroccan plant in Kenitra is certainly a further positive step for the company in terms of its electrification strategy. Now, thanks to this significant investment, the automotive group will be able to increase the production of both hybrid and electric vehicles. A further contribution to reducing CO2 emissions for the future, promoting sustainable mobility.