Stellantis’ actions toward sustainable mobility are continuing, and one more step was recently delved into regarding the transformation of its paint shops for production cars. These environments are known to normally have a rather high environmental impact due to the products that are used. Now, however, they are becoming truly innovative laboratories, which are laying their foundations on energy efficiency and emission reduction at the heart of all kinds of processes that take place within them.
Sustainable paint for Stellantis workshops
Stellantis has a carbon neutrality plan that it is expected to achieve by the year 2038. This strategy, as discussed on several occasions, relates to every step in the production cycle of the group’s cars. Now in fact, it is the turn of the paint shops. Environments that within a facility cause a very high energy expenditure, but will now become the focus of a major sustainable innovation.
As anticipated, paint shops around the world, have always been considered as a very weak point regarding the environmental impact of the automotive industry, and not only that, also harmful to the human being working there. Now Stellantis, has decided to reduce the energy consumption of all these facilities by 50 percent, all by the year 2025, taking the year 2021 as a benchmark. How could this big change happen in such a short time? By simplifying production processes, making the machinery needed for processing electrical, and providing workers with completely innovative materials.
Energy efficiency optimization in coating processes
In more detail, that which should happen the following. It starts with a discussion of fewer steps, more savings, that is, the reduction of baking operations during the coating process. The intent is to move from a process that currently involves two wets, to one that involves four, a way to reduce energy consumption by about 30 percent. Second step is to use green electricity instead of fossil fuels. Generally, drying kilns that have always been powered by natural gas are slowly transitioning to renewable electricity. This kind of transition is combined with a number of other initiatives such as, for example, air recycling in the spray booth.
The result should be optimized energy efficiency, substantially reducing CO2 emissions. Finally, the use of innovative materials for the industry. This includes the provision of new types of sealant, paints, and low-bake coatings that generate additional energy savings. For example, E-coat technology that is done by slow baking, which was introduced in France, has now spread to all Stellantis Group plants, making a valuable contribution to overall savings.
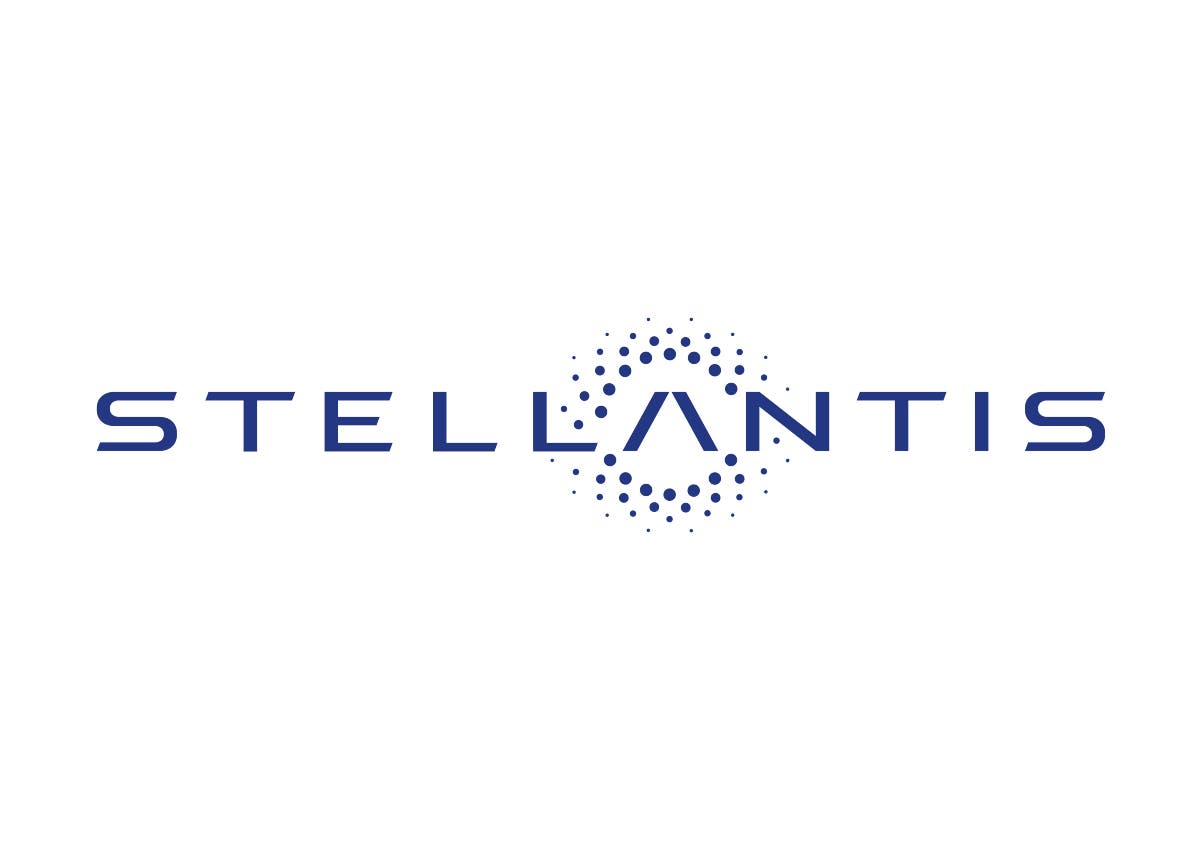
The new coating and the current results achieved
The first results of this strong innovation are also already very visible in numerical terms. The Gliwice plant located in Poland has achieved an energy consumption of only 245 kWh per vehicle produced, a benchmark for the entire industry. By the end of this year, 70 percent of all Stellantis Group plants are expected to be converted to use the new four-stage process.
The plant from which major milestones in this area are currently expected is the Sochaux plant in France. This will be a zero-carbon environment, completion structured to be at the forefront of all available environmentally friendly technologies. This plant will come into operation in 2025, representing the emblem of Stellantis’ worldwide strategy to revolutionize plant paint departments. Should the next steps all go well, it could even be the automotive group’s first carbon-neutral paint shop in the world.