This investment, which introduces Moving Ground Plane (MGP) technology, expands Stellantis’ wind tunnel capabilities, enabling it to measure and reduce aerodynamic drag caused by wheels and tires, a factor that accounts for up to 10 percent of total friction in the real world. In this way, Stellantis aims to improve the efficiency of its electric vehicles, increasing their range and potentially reducing battery size. Integrating artificial intelligence into this process ensures greater accuracy and automation, accelerating product development. MGP technology is a key element in Stellantis’ Dare Forward 2030 strategic plan, supporting its ambitious vision for a zero-emission future.
Move Ground Plane, huge investment
In a press release dated today, Oct. 23, Stellantis unveiled its innovative Moving Ground Plane (MGP) technology, a $29.5 million investment, at the company’s research and technical center in Auburn Hills, Mich. The enhanced wind tunnel will be able to measure and reduce airflow resistance from wheels and tires, which can account for up to 10 percent of total drag in the real world. Optimizing aerodynamic efficiency is critical in the effort to extend the driving range of electrified vehicles on a single charge. This improvement directly contributes to greater efficiency, benefiting customers with longer EV ranges and potentially reducing battery size, which in turn could lead to cost and weight savings.
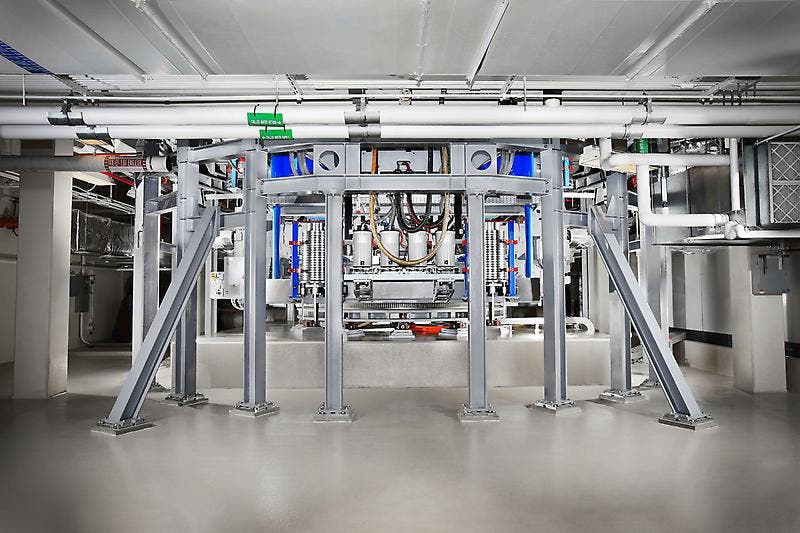
“Range is a key consideration for customers who are transitioning to cleaner mobility via battery power,” said Mark Champine, senior vice president and head of North American engineering technical centers. “That’s what makes this investment so critical. By reducing drag, improving the range of electric vehicles and ultimately the overall customer driving experience.” The upgrade to the company’s innovative aeroacoustic wind tunnel simulates a real-world ride while allowing test vehicles to remain static. Straps suspended from air cushions allow wheel movement on all four corners, while a fifth strap runs longitudinally under the vehicle, mimicking road travel conditions. This realistic simulation allows for more accurate testing and aerodynamic improvements
“For electric vehicles, increased range enabled by improved aerodynamics can lead to potential reductions in battery size,” Champine said. and again: “This has positive implications from more efficient savings between packaging and weight that will ultimately improve the customer experience.”
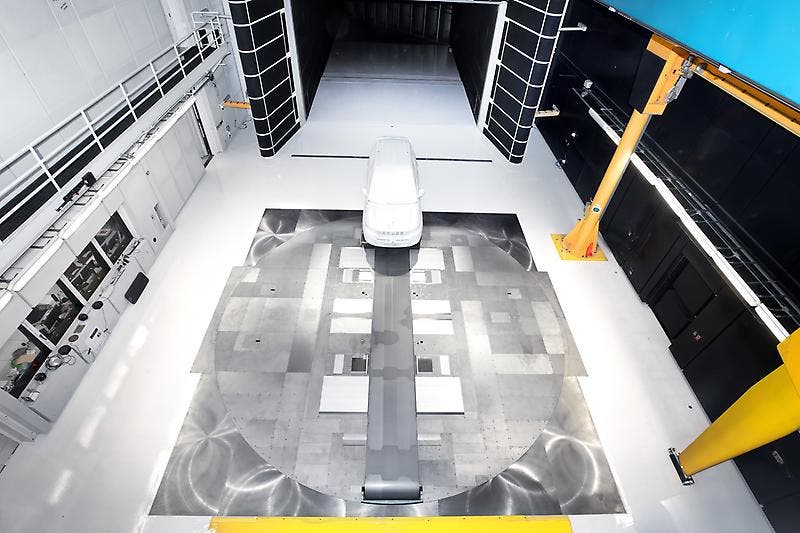
Benefits for multiple Stellantis brands
The investment in MGP technology will benefit multiple Stellantis brands, regardless of where they are sold or how they are powered, and will benefit from aerodynamic optimization. The updated wind tunnel also provides a valuable complement to the virtual development tools. “This apparatus is a great addition to the virtual tools, which may not take into account factors such as tire deformation that can compromise aerodynamics,” Champine said. “With this technology we can replicate such conditions and capture real-time data to explore solutions.”
The new facility also adds an essential automation capability. Pitch and track test modifications, which can take up to two hours in conventional wind tunnels, can now be performed in minutes. The combined result of real-time data collection and increased automation: increased speed to market.
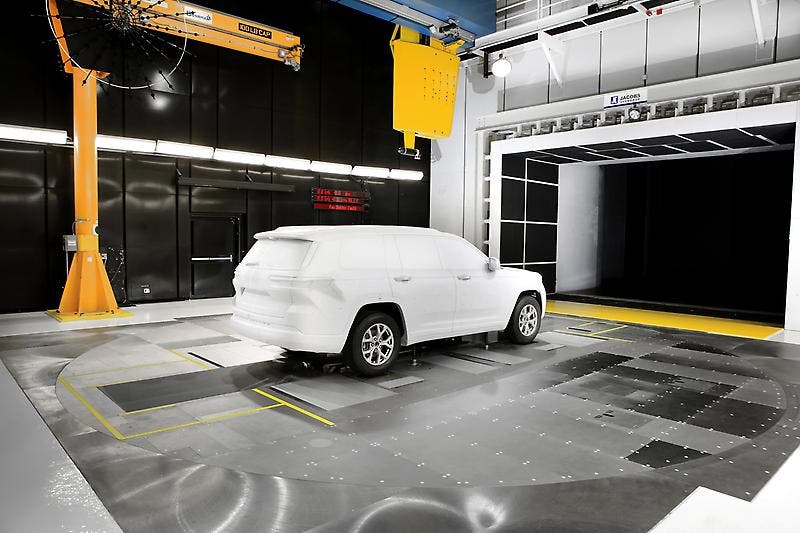
Auburn Hills at the heart of the project
While Stellantis uses MGP technology in other facilities around the world, those sites are focused on smaller vehicle platforms. The improved Auburn Hills facility will be able to accommodate larger vehicles, particularly those based on the STLA Large and STLA Frame platforms. MGP technology is a key factor in BEV development, as outlined in the company’s Dare Forward 2030 strategic plan , and will account for 50 percent of Stellantis sales in the United States and 100 percent of European sales by 2030. Globally, Stellantis aims to offer more than 75 BEVs by that date, accounting for 5 million vehicles sold annually.
This investment underscores Stellantis’ commitment to achieving zero net carbon emissions by 2038 as part of its leadership in climate change mitigation. The modernized facility is part of an estimated $85 million commitment included in the 2019 UAW contract. It includes a new annex for staging test vehicles and a new outbuilding to support the MGP system, which uses high-pressure compressed air to drive wheel and center belts at speeds up to 140 mph. The entire process is carefully controlled by electromechanical actuators. The measuring platform and turntable that form the heart of the MGP equipment weigh 137 tons, rest on a concrete foundation and are supported by a specially designed steel frame. The wind tunnel, capable of generating wind speeds of more than 160 mph, has been in continuous operation since 2002.