Stellantis joins global MSD Pledge 2.0 initiative and improves ergonomics to reduce injuries. Stellantis has announced yesterday Oct. 24 its membership in the MSD Pledge 2.0, a global initiative to improve worker health and safety. By joining forces with 200 other organizations, the company pledges to significantly reduce musculoskeletal disorders, a leading cause of workplace injuries.
Stellantis aims for worker well-being
In recognition of National Ergonomics Month, Stellantis announced on yesterday’s Oct. 24, 2024, that it has signed the MSD Pledge 2.0, an initiative of the National Safety Council (NSC) that aims to improve the well-being of workers in various industries while reducing musculoskeletal disorders (MSDs), a leading cause of workplace injuries.
The pledge is an outcome of the MSD Solutions Lab, an innovative NSC program established in 2021 with funding from Amazon to focus on combating MSDs. It invites organizations of all sizes to commit to the core community goals of the pledge to reduce the risk of MSDs for millions of workers.
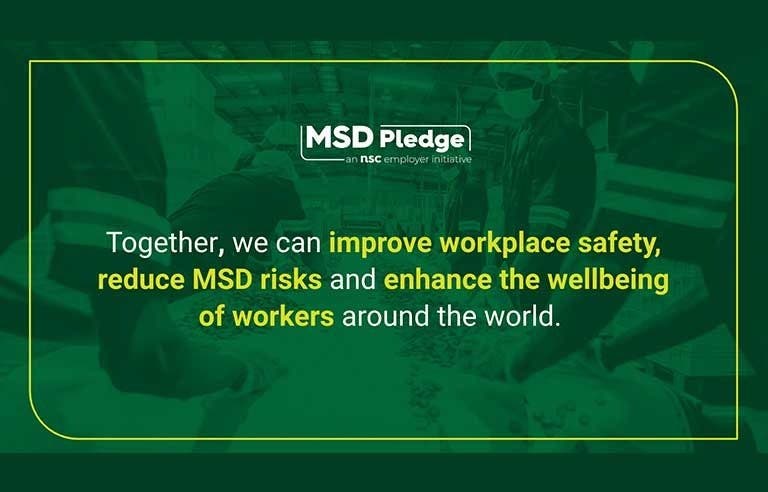
“By signing the pledge, Stellantis is demonstrating its commitment to identifying and reducing MSDs while promoting a culture of safety in our North American facilities,” said Garrett Stricker, director of corporate health and safety at Stellantis. “We also gain access to additional insights, knowledge and best practices from 200 other organizations, along with access to cutting-edge safety technologies to greatly improve the lives of our employees.”
According to the World Health Organization (WHO), DLMs are the most common workplace injuries and a leading cause of reduced employee work years, surpassed only by mental illness and substance abuse. These injuries are also costly, resulting in lost wages and medical expenses for private U.S. companies each year of nearly $17 billion.
Ergonomic approach to improving working conditions
Stellantis’ approach to ergonomics focuses on improving the workplace-worker interface through the integration of standards, identification of ergonomic risk, and effective solutions using advanced tools such as digital human modeling software and virtual reality in the early stages of process design. This includes cross-functional involvement with joint health and safety teams and at all levels of the organization, from management to the production department.
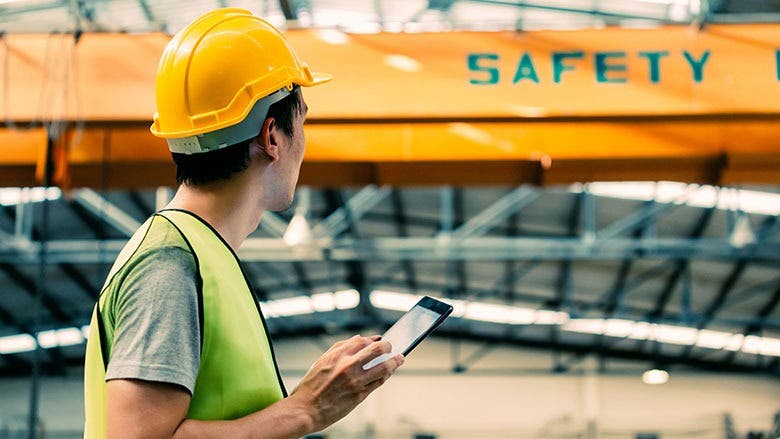
In 2023, a new ergonomic risk assessment tool was introduced at Stellantis’ manufacturing and non-manufacturing sites. The software uses artificial intelligence (AI) motion capture video technology to assess jobs/activities, identify risk factors, improve the efficiency of assessments, and provide meaningful results to reduce overall risk and improve well-being, health, and safety. In addition, the focus on standards, best practices, innovation and new technologies, including collaboration with industry partners United States Council for Automotive Research (USCAR), continues to improve efficiency and accuracy in identifying and reducing ergonomic risk. This is something that should provide greater peace of mind in all respects for the company and its workers.
Going forward, the effort aims to strengthen MSD’s corporate ergonomics program and prevention efforts with a continued focus on risk reduction, innovation and collaboration. It will also build on the organization’s existing safety culture to improve the overall well-being, health and safety of the workforce.