This is one of the most modern crash test centers in the southern hemisphere. Located at the Stellantis Betim automotive complex in Minas Gerais, the space is designed to ensure the necessary legal and technical certifications for all projects developed and applied for the company’s brands, reaffirming its commitment to offering customers products with the highest vehicle safety performance.
1,000 crash tests conducted at Betim Safety Center
“The Safety Center is now one of the company’s most modern crash test centers and commitment to South America The milestone of 1,000 tests conducted at Betim reflects our commitment to innovation, technology and, most importantly, to people and consumers. The combination of these factors has enabled Stellantis to anticipate the future of consumers, offering modernity, performance and safety,” emphasizes Emanuele Cappellano, Stellantis president for South America.
“Our goal is to offer customers products that provide the highest level of performance in terms of vehicle safety. To achieve this goal, we conduct more than 200 tests per year in Betim. The entire process is conducted with the rigor required by global standards. During impact simulations, all designs developed for Stellantis brands must fully meet the requirements set by international standards, with no margin for error,” says Márcio Tonani, senior vice president of Stellantis Technical Engineering Centers for North America South.
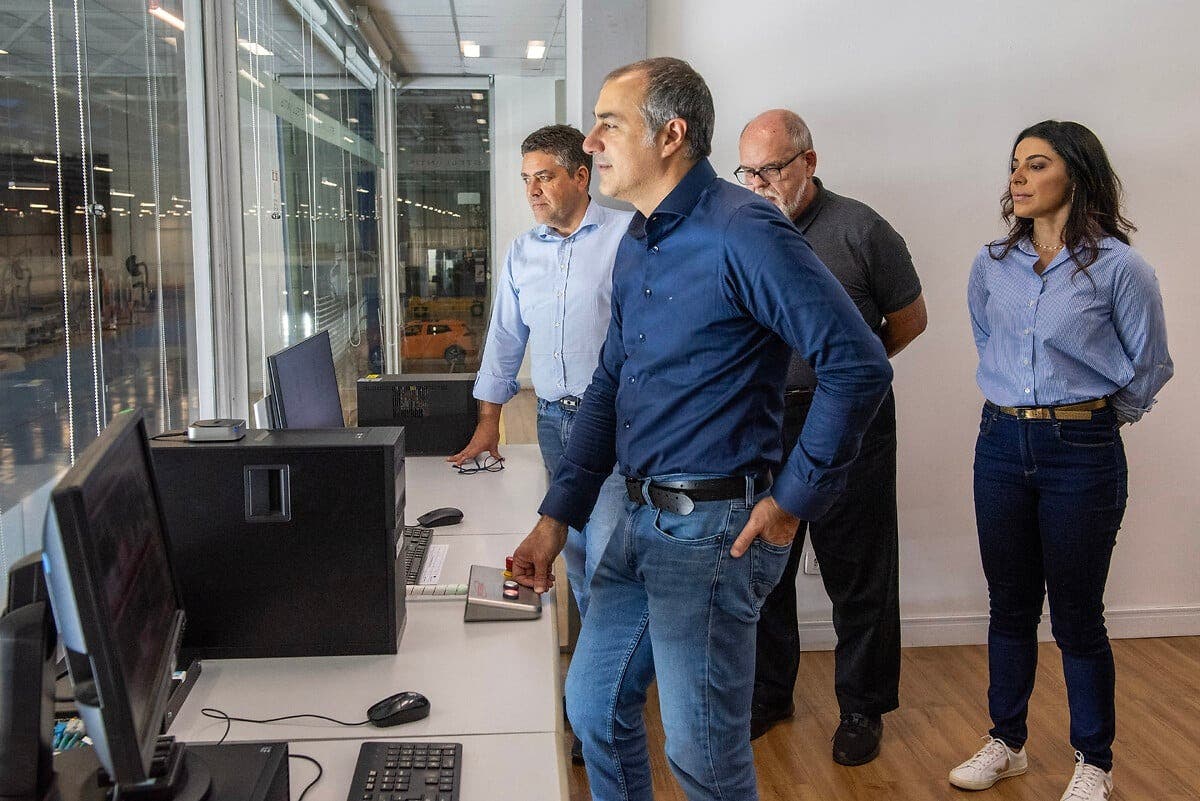
The Safety Center’s specialized team of more than 50 engineers
The crash test is developed in two stages by the Safety Center’s specialized team of more than 50 engineers. In the first phase, which precedes the crash, a detailed analysis of all aspects related to vehicle safety is carried out. This phase includes procedures such as removing fluids from the vehicle, static measurements, installing sensors, painting specific areas for impact analysis, and setting up the cameras responsible for accurately recording the effects on the vehicle and on dummies, anthropomorphic dolls that simulate human body responses in impact situations.
In the second stage, after impact, all data generated during the test are recorded and thoroughly evaluated. This process is essential to ensure the accuracy and consistency of the results, which follow strict global vehicle safety standards that guarantee the suitability and reliability of the process. From detailed vehicle preparation to final analysis of results, each crash test requires more than 250 hours of specialized labor, reflecting Stellantis’ commitment to excellence and safety in all its products.
Safety Center, 100% technology autonomy
Installed in 2019 at the Stellantis Automotive Hub in Betim, the Safety Center has brought 100 percent technological autonomy to the region, enabling it to meet all stages of new vehicle development. The center is responsible for the design, development and testing of world-class vehicles in South America, with a high level of quality and excellence.
The complex has an area of 7,600 m² and a 130-meter track, with the capacity to conduct impact tests on vehicles weighing up to 4 tons. It was developed to conduct frontal, rear and side impact tests against rigid and deformable barriers, with international standard tests covering all homologations. In addition, on-site physical tests evaluate not only the structure of cars, but also restraint systems, such as seat belts and airbags, replicating a wide variety of crash scenarios.
Over the course of five years, the Safety Center has received numerous technological innovations to raise vehicle safety standards. In 2023, the Dummies Certification Laboratory was opened, developed by the Stellantis global team in Brazil to certify dummies used in the highest-level crash tests in the region.
The new laboratory plays a key role in individually testing each part of the dummies. The anthropomorphic dolls are equipped with about 50 strategically placed sensors, which enable precise analysis of how the human body reacts in different types of accidents.