The race to reduce costs in the automotive sector continues, and Stellantis is studying additional solutions to make its production increasingly cost-effective. In recent days, the automotive group led by Carlos Tavares announced the internalization of plastic injection at the Rennes-La Janais facility. Modularity, which has characterized the automotive industry, thus seems to have reached its limits with the advent of electric vehicles.
Stellantis wants to internalize the production of some components to reduce costs and increase profit margins
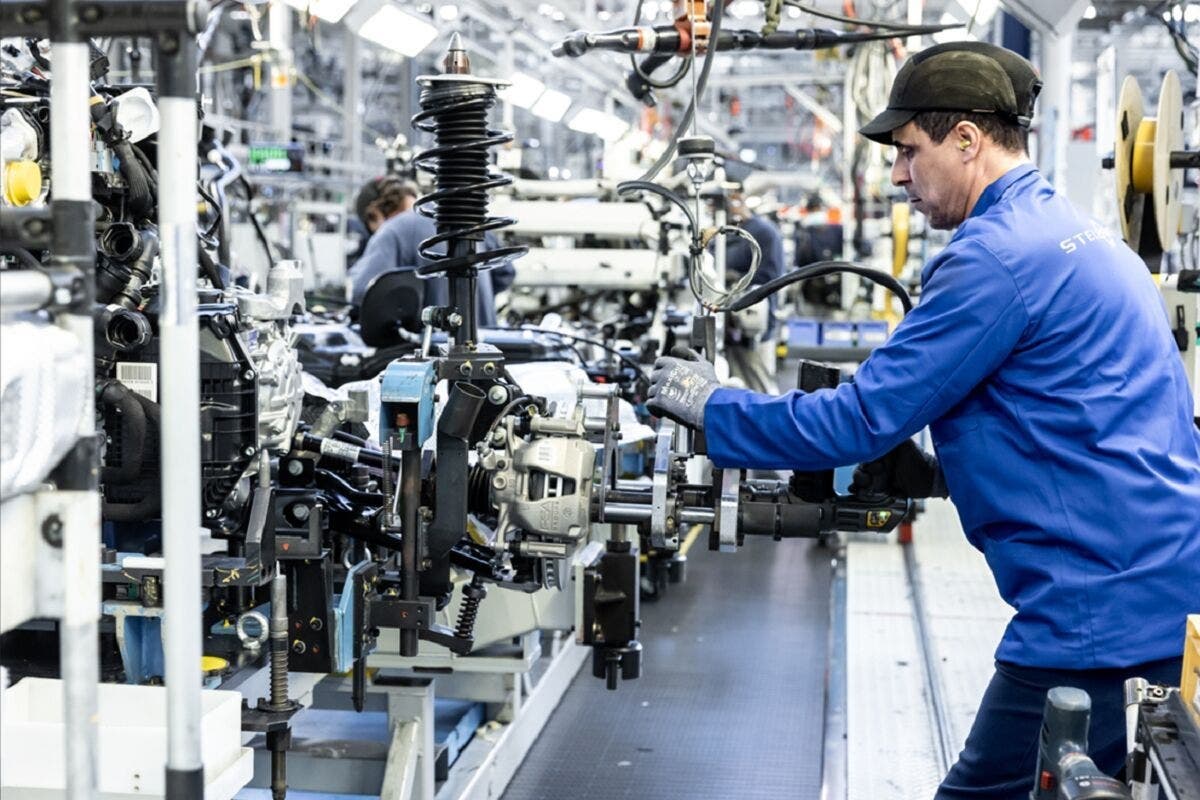
“We have been observing a decline in the prices of raw materials used in electric vehicles for some time,” the manager recalled during a visit to the Stellantis Rennes factory for the launch of the new STLA Medium platform. “This helps reduce costs, mainly because the demand for these vehicles isn’t as strong as expected. This is a positive effect, as raw material costs are lower than anticipated. However, we must hope this provides the necessary time to create new production capacity to avoid price increases if demand should rise. This remains a volatile element that we don’t fully control,” he added.
“To further reduce electric vehicle costs, we need to explore new ways,” explains Carlos Tavares. “25 or 30 years ago, the industry experienced a movement toward modular outsourcing: modules such as seats or the front panel were entrusted to suppliers, considered more efficient than the manufacturers themselves. At the time, this approach seemed obvious. But today, after evaluation, we often see that our internal teams are more efficient, both in terms of costs and quality.”
Carlos Tavares added: “This internal efficiency represents higher profits. We’re trying to achieve an electric vehicle cost comparable to that of thermal vehicles to offer competitive prices to our customers. However, it’s not about returning to the extremes of the 1950s, where everything was internalized. We need to find the right balance to maximize benefits.”
Based on Fiat‘s experience in Italy at the Melfi plant, the manufacturer has decided to internalize a workshop dedicated to plastics, bumpers, door protections, and fenders. Installed in a workshop previously reserved for painting, plastic injection was made possible thanks to the repatriation of six presses from Italy. This workshop is part of the production of the new CR3 model produced on the multi-energy STLA Medium platform.