Stellantis aims for a zero-emission future with recycling at its core. And this news demonstrates a concrete commitment to sustainability in line with EU Directive 2031 on the use of recycled materials. SUSTAINera, the dedicated subsidiary, creates a complete recycling supply chain for end-of-life components, batteries, and vehicles.
Stellantis: circular economy at the heart of Dare Forward 2030 with a focus on recycling
Stellantis as we well know never ceases to amaze. In fact, the automotive group not only works as a car manufacturer, but is also particularly active in the area of recycling. In fact, the company has confirmed several times its commitment to a more sustainable future by investing heavily in the recycling of components, batteries, and end-of-life vehicles.
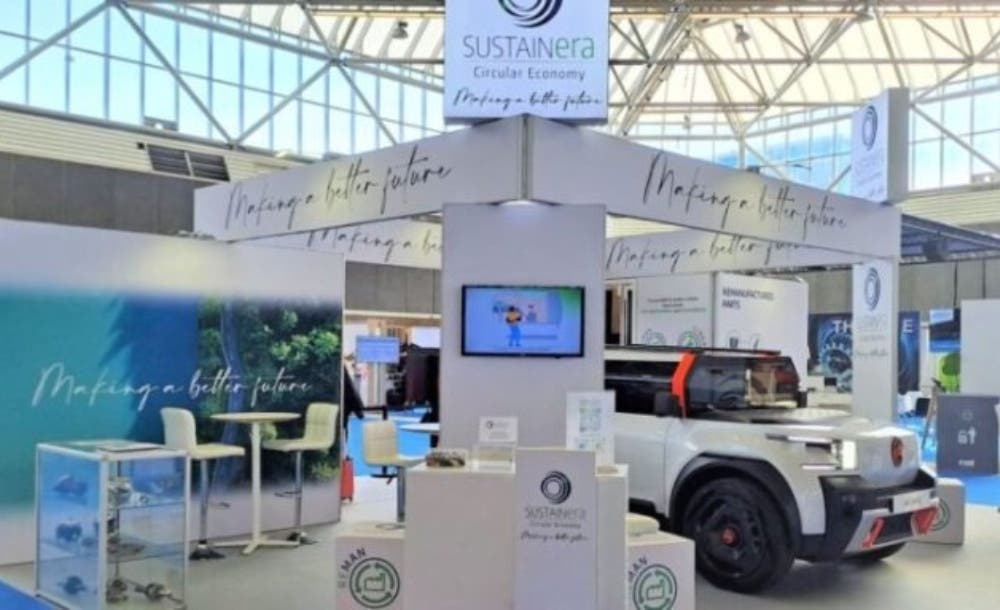
Thanks to the Circular Economy unit and its subsidiary SUSTAINera, Stellantis now aims to rapidly raise recycling revenues by 2030, roughly reaching a total of more than 2 billion euros. Which comes across as a rather ambitious challenge, but one that fits perfectly into the Dare Forward 2030 strategic plan.
A concrete example of the work Stellantis does in this regard is Valorauto. That’s the platform dedicated to the management of end-of-life vehicles. It is active in France, Belgium and Luxembourg, where it offers a comprehensive service free of charge to both private customers and dealers. The service includes the ability to take back any type of vehicle (gasoline, hybrid, or electric) and ensure an adequate economic return for users who use it.
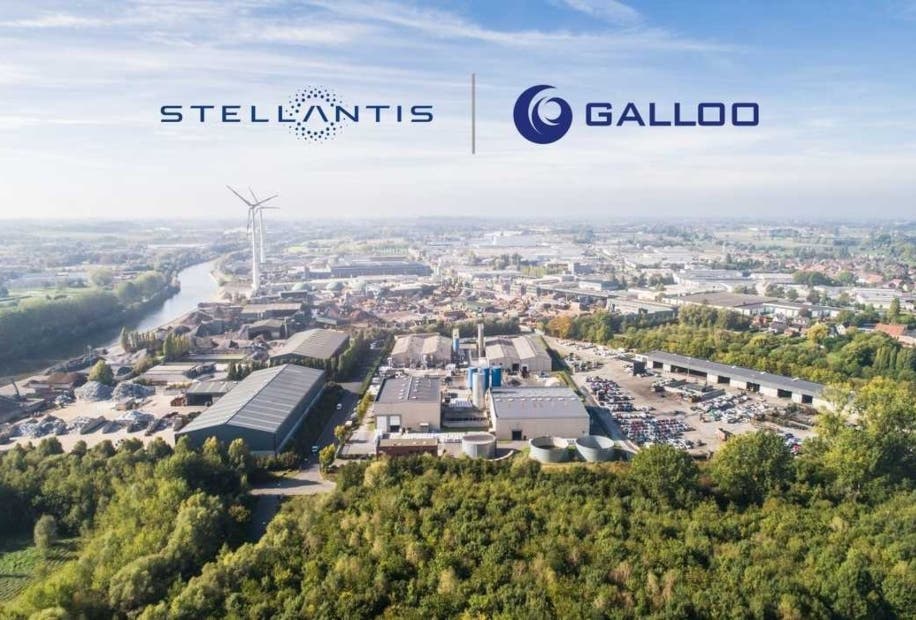
Valorauto is familiar as the operating arm of the SUSTAINera Valorauto SAS joint venture between Stellantis and Galloo, the absolute leader in automotive recycling. Their main corporate goal is to offer a complete solution for all those vehicles that reach end-of-life. This is a process that provides a virtuous cycle for the car. In fact, Valorauto, thanks to a series of authorized treatment centers, initially takes care of the collection and dismantling of the car in question.
Subsequently, parts that are still functioning, including batteries of electric vehicles, are recovered and reused. In fact, they are also included in second-life projects as energy accumulators. All other materials are recycled properly, respecting the environment in every respect, just as the circular economy also requires. This process fits perfectly into Stellantis’ circular economy goals, which include extending the life cycle of each individual product, making sure that materials are put back into circulation at the end of their life, with the ultimate goal of drastically reducing waste and working positively for the environmental impact. In addition to this, economic value is also created for those who use the service and the European Regulation on Extended Producer Responsibility for vehicles is complied with.
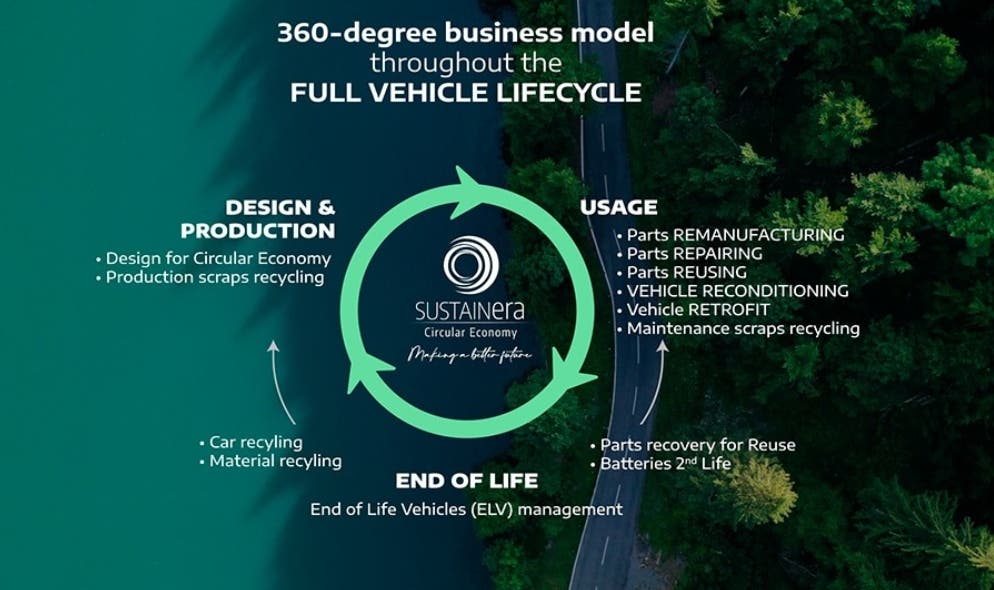
To comply with the French circular economy law (Loi AGEC), Stellantis has developed an Individual System dedicated to the management of its end-of-life vehicles. This system ensures the quality of the process at every stage, from eco-design to scrapping, contributing to the development of a virtuous circular economy within the group. The goal is to extend this model to other countries, in accordance with current regulations, and to expand Valorauto’s services to major European markets.
As is now well understood, we know that Stellantis embraces the philosophy of the circular economy with great enthusiasm, working hard to give a new life to materials that would be destined for waste. At the heart of this vision is the revolutionary SUSTAINera program, which closes the loop on several production chains.
One very impactful example is certainly the recycling of alloy wheels in the North American market, in partnership with Real Alloy. Wheels that have reached the end of their life are collected by distributors and retailers and are then transformed into raw aluminum through casting plants at Kokomo. The aluminum that is obtained is then used to create engine and transmission components, thus preventing the waste of material that was previously unusable.
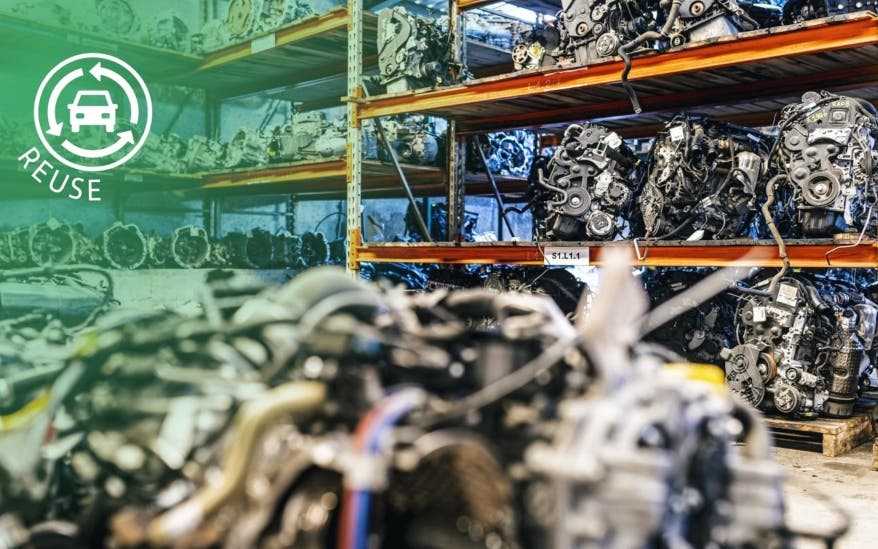
Taking inspiration from the 4R principles (Spare, Repair, Reuse, Recycle), SUSTAINera has launched its first range of recycled products. It includes windshield washer fluid and coolant. The former is made from 100 percent alcohol that has been regenerated from recycled industrial solvents. This environmentally friendly product not only greatly reduces waste but also ensures excellent performance. Its special formula that does not include dyes is able to guarantee flawless windshield cleaning and frost protection down to -20°C.
As for the refrigerant fluid, on the other hand, it is produced based on 100% recycled monoethylene glycol from industrial production waste. It is a fluid that does not contain nitrates, borates, amines and silicates but is able to protect the engine from rust, overheating and freezing (down to -25°C). Its characteristics make it perfectly compatible for use in Stellantis and other brands of vehicles. The first products of this kind strictly adhere to the specifications of the various manufacturers and are available in different formats from both professionals and individuals. To top it off, the packaging is made from at least 50 percent recycled plastic.
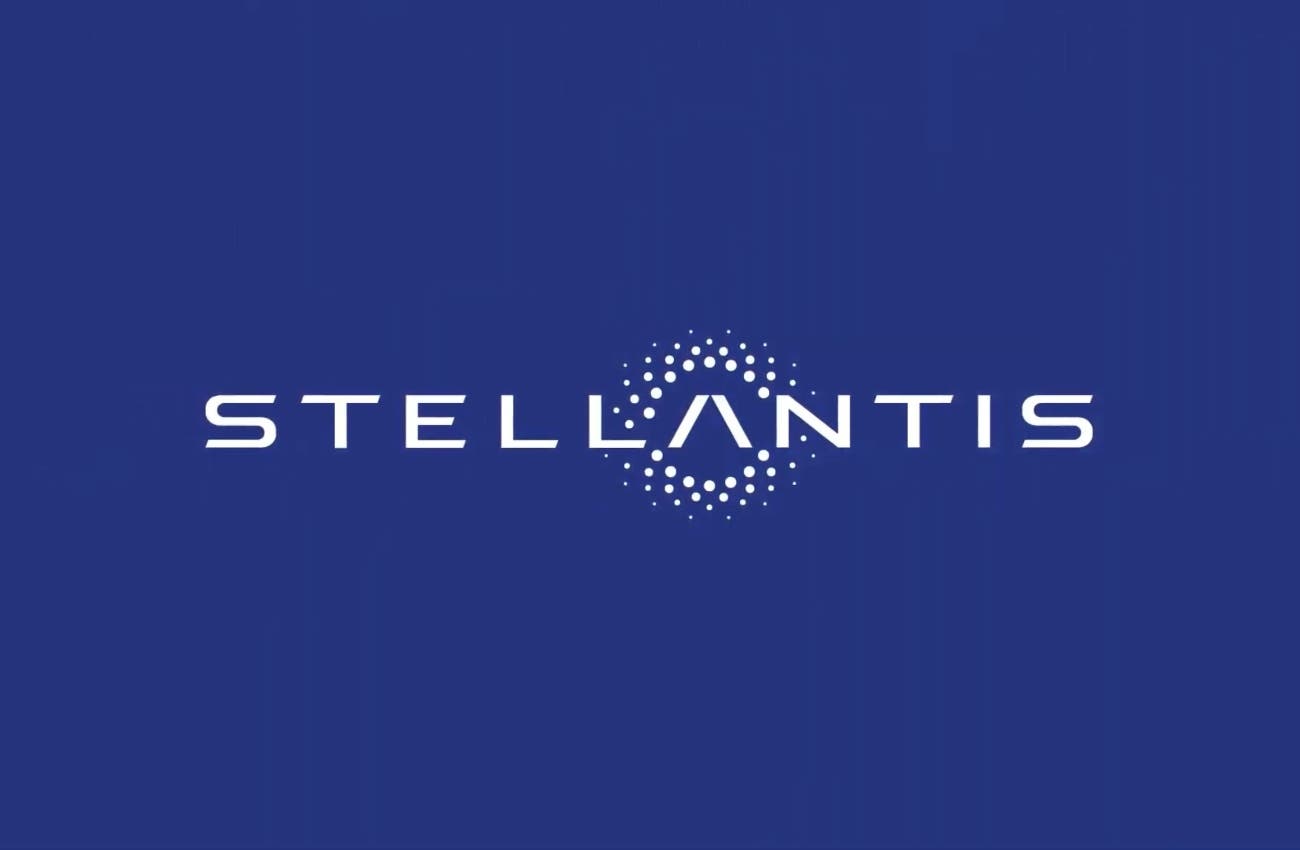
Additionally, Stellantis has signed an MOU with Oran to create a joint venture dedicated to recycling end-of-life batteries from electric vehicles and scrap from gigafactories in Europe and North America. This partnership gives Stellantis the opportunity to recover cobalt, nickel, and lithium, which are all valuable elements for the creation of new batteries, in line with EU Directive 2031 on the use of recycled materials. The Stellantis company is therefore committed to reducing its environmental impact at all stages of the production cycle, from design to material procurement and waste disposal.